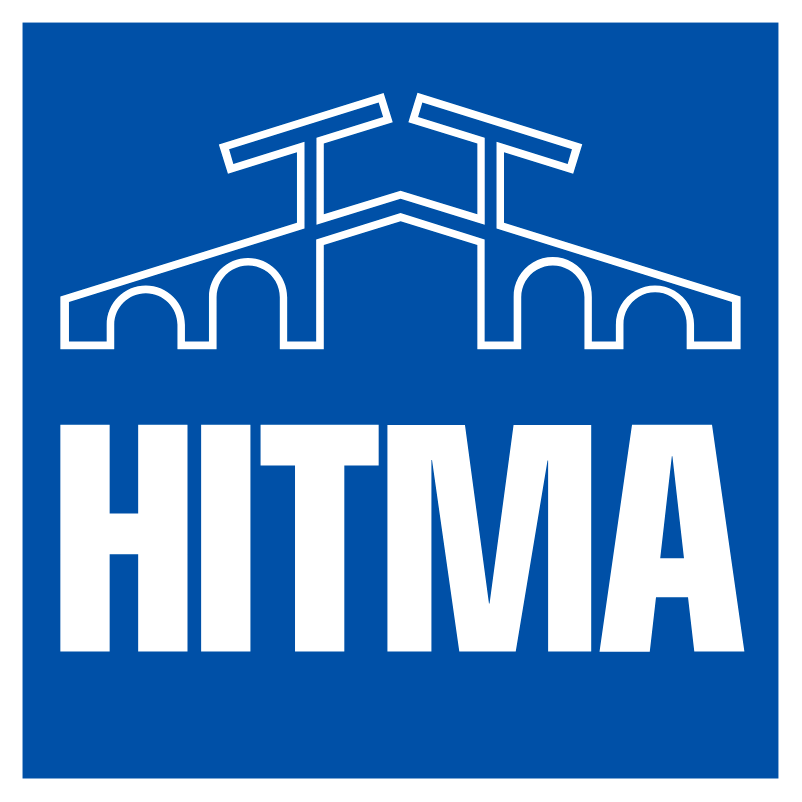
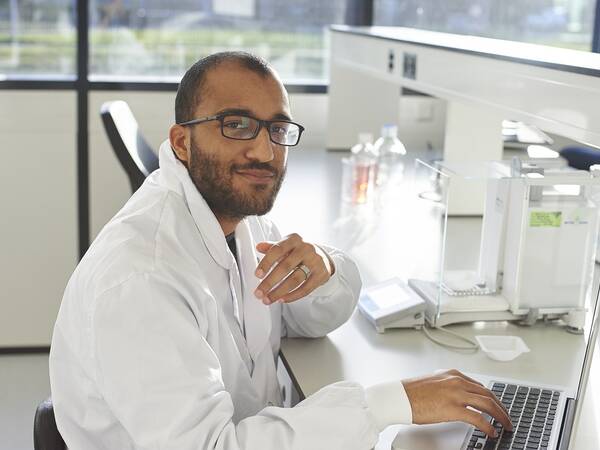
Strict requirements and time constraints are really speeding up the use of single-use technology.
Over the past 10 to 15 years, the adoption of single-use technology in the life-science sector has gained enormous momentum. Where at first people were still sceptical about whether single-use technology can be deployed for biopharmaceutical processes, the word ‘whether’ can now be replaced with ‘how’. In the past few months, I also noticed this during large events for the biopharmaceutical sector, such as Disposable Solutions for Biomanufacturing in Munich, the Interphex in New York and recently BioProcess International in Amsterdam.
Smarter and faster
Now that the ‘medicine landscape’ is so diverse, there is a greater need for efficiency in order to speed up the process from idea to end product. The biopharmaceutical industry is therefore deploying single-use solutions more and more often, and this is making the production processes smarter and faster. And not only the pharmacy but also the patient is benefiting from this.
Vision of pharmaceutical companies
An interesting article was published about the vision of large pharmaceutical companies in the United States regarding the future of single-use (Evolve With Flexibility: Advancing Single-Use Technology With Industry Collaboration). In the article, I read that Morgan Norris, General Manager Upstream and Cell Culture at GE Healthcare, believes that single-use biomanufacturing strategies can offer the biopharmaceutical industry more benefits than ever.
Overcoming challenges
The same article stated that people at Merck & Co in the US are convinced that a once-off production facility is more cost-effective than stainless steel, regardless of the requisite capacity. However, Jeffrey Johnson, New Technology Lead and Director at Merck, advocates greater collaboration in the pharmaceutical sector to overcome the challenges.
Capacity expansion
Fujifilm Diosynth Biotechnologies in the US are also focusing on growth using single-use technology. Where they used to use stainless steel installations to develop their medicines, the need for capacity expansion inspired them to explore alternatives. Stainless steel was too expensive and it took too much time to set up and build production systems.
Which is why Fujifilm started researching the possibilities of single-use. They realised that single-use technology would help them reduce the costs and speed up the development of medicines. But would it still offer the same quality as stainless steel as far as cell growth, cellular productivity and product quality are concerned? By studying this, Fujifilm accumulated an enormous amount of knowledge and as an early adopter they were able to expand their capacity and focus on new developments.
Rapidly-growing sales market
Pfizer (US) experienced the advantages of single-use technology when, due to a rapidly-growing sales market in China, they wanted to quickly launch their medicines on the market there. They succeeded in doing this and they also managed to reduce their costs.
Single-use is sustainable
Besides efficiency, sustainability also plays an important role, of course, in the choice for single-use technology. In the past decade, the pharmaceutical industry has come under enormous pressure, especially in terms of reducing the burden on the environment. Single-use technology reduces the use of water and cleaning materials. Needless to say, that’s a positive development for the environment.
Surprising results
GE Healthcare Life Sciences conducted research into the burden on the environment and looked into systems for once-off use versus conventional production systems. In a study in the US, they compared the environmental impact of single-use compared to stainless steel based on 18 points. The results may surprise some people: In a production process of monoclonal antibodies in volumes of 100, 500 and 2,000 litres, single-use technology scores considerably better than traditional stainless steel. To be precise, in this study single-use scores positive on all components related to environmental impact.
Energy and water savings
The results of these types of studies are changing the industry’s view of single-use when it comes to sustainability. The environmental benefit of once-off technology compared to traditional stainless steel process technology mainly involves the considerably lower energy and water requirements when the need for extensive cleaning and sterilisation between every batch production is eliminated. The reduced use of chemicals also plays a role.
Open communication and reliable partners
Large pharmaceutical companies are therefore achieving good results with single-use systems. One thing that the pharmaceutical companies in this article in any case have in common is that they are aware of the importance of open communication throughout the supply chain. And the development of single-use production systems runs smoothly when you work with reliable partners that know what they are doing.