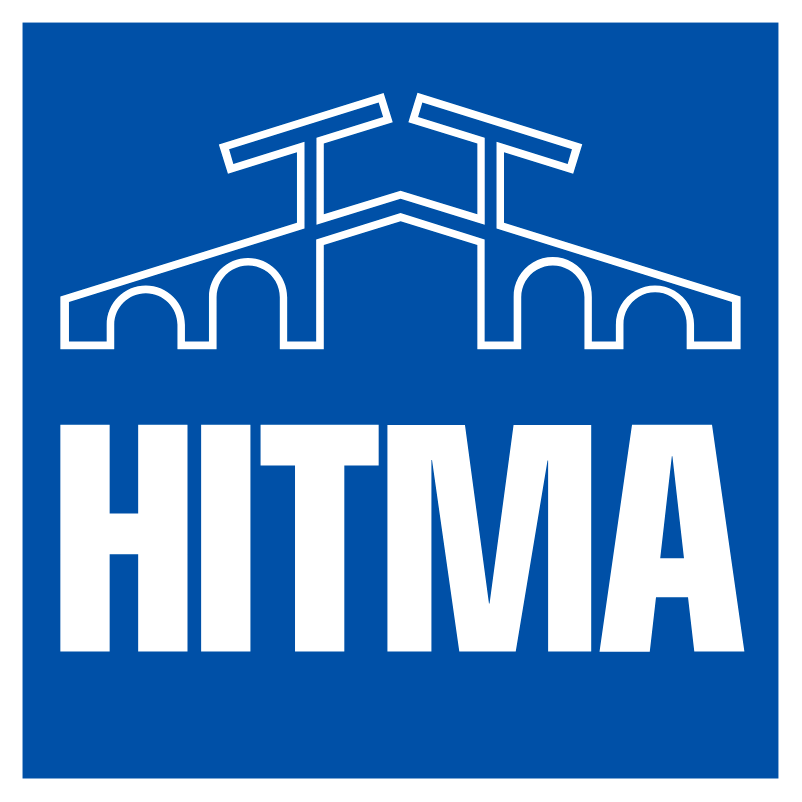
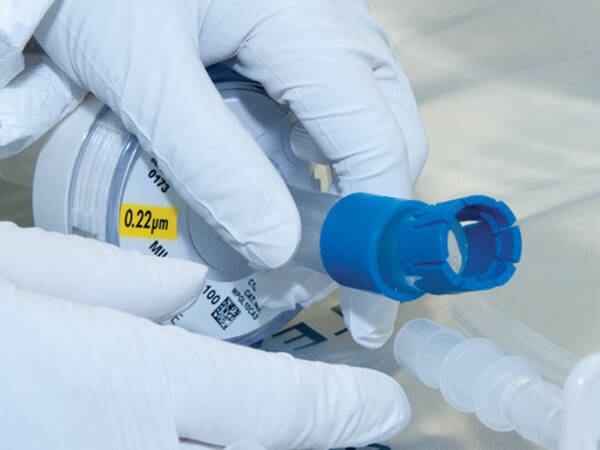
How do you optimise the flow path of a filtration step?
Filtration steps occur frequently in biopharmaceutical processes. They include such things as clarification, buffering and concentration of a product with TFF (tangential flow filtration) or the filtering of an intermediary and the sterile filtering of an end product with NFF (normal flow filtration). As during every step, here there are a number of things that must be taken into account to arrive at a successful result.
Potential risks during a filtration step
During filtration, the main risk involves the possible pressures you can create. The higher the pressure on the system, the greater the chance that expensive products will leak. A filtration flow path often includes numerous connection points in order to make the system as versatile as possible. These connection points, together with the tubing that is used, must always be able to resist the expected process pressures. It is therefore crucial that the right components are chosen. At very low pressures, standard solutions are often the best choice. When the pressures rise, adapted components are the ideal solution. I’m mainly thinking of braided tubing, hoses and reinforced connections, such as BarbLock.
A second risk is that the integrity of the filter can be affected due to an excessive peak pressure. Certain particles are then no longer kept out and they enter the filtrate. This can have very negative effects on the quality of the product. To prevent this, the filtration step should be implemented with pressure control. As soon as the pressure has reached the maximum pressure of the weakest component, the pump is actuated to pump slower (or stop) so that the pressure normalises.
Testing filter integrity
It is wise to test the integrity of the filter after every filtration step. One easy way of doing this is to conduct an NWP test (normalised water permeability test). The ‘NWP specification’ is often enclosed with the filter packaging. If the measured NWP is significantly higher, there is a good chance that the integrity of the filter has been compromised.
Choosing a single-use or multiple-use flow path
There's no denying it any more. The pharmaceutical sector is tending more and more towards single-use solutions. So there are strong arguments for opting for single-use even when building a flow path. Firstly, the use of single-use components saves an enormous amount of time, given that cleaning procedures are no longer necessary and only limited preparatory work is required. Secondly, single-use solutions offer much more flexibility. So it is much easier to find a tailor-made solution for every process. Also, and this is perhaps the most important argument, the chance of cross-contamination is eliminated.
Nowadays it is easy to build a completely disposable flow path. There are single-use sensors available for measuring process parameters such as pressure, flow rate, turbidity and conductivity. Disposable flow meters can be used to measure the flow rate. For pumps, there are disposable pump heads such as those used in the diaphragm pumps from Quattroflow.
Finding your way among the possible options
Based on my biotech experience, I know only too well that finding the best solution for a specific process can be a huge challenge. There are so many possibilities that sometimes it’s difficult to see the wood for the trees. Which tubing or hose is the best fit for my process? How do I connect them to my system? Is there a chance of leachables or extractables? Should you choose a ready-to-use solution to save extra time and guarantee the quality of your flow path? Then you can outsource the assembly of the flow path.
Custom filter assemblies
At Hitma, we have an ISO class 7 cleanroom. There, our experienced employees can assemble the various components that were chosen for your filtration step. That means that we can provide a ready-to-use solution. This solution is packaged using the packaging of your choice (single-bagged or double bagged) and always delivered with the necessary certificates. If you want the assemblies to be tested for leaks (gross leak test), or you want them to be delivered gamma-irradiated, we can also do that for you.
In that case, we will invite you to join us at the drawing board. Where we can discuss the various requirements to be met by the components for your filtration step. That way, we select the best solution together.