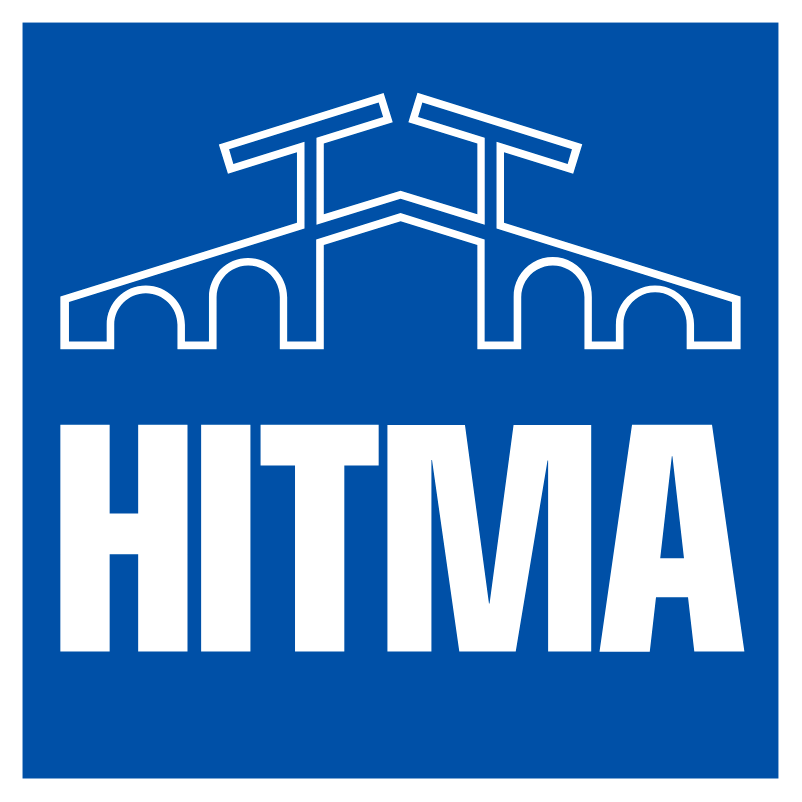
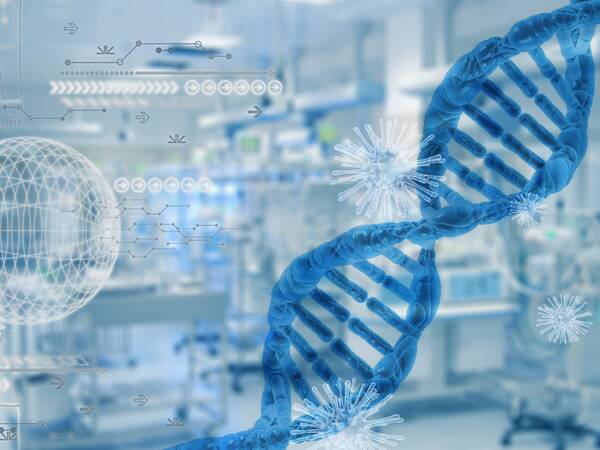
Developing vaccines; choose single-use at the start for all phases of the process
With the world on the hunt for a coronavirus vaccine, now is the ideal time for me to write a blog about the rapid development of vaccines and the role of single-use technology in this process. My main focus is on the importance of choosing the right single-use process materials at the start of the development process; as early as possible in the first research phase.
Shorten vaccine development time
Normally, it takes five to ten years before a vaccine against a new infectious disease is available. Before the vaccine is ready, the process goes through various research, testing and process steps. Around the world, researchers are trying everything to shorten this development time. Single-use technology attributes to this. Disposable components and assemblies are used throughout the entire biopharmaceutical process; from the laboratory till the moment that a working vaccine can be produced on large scale.
Wrong choice, huge consequences
It is well known that choices for single-use technology made early in the process, can have huge consequences later after it is decided to up-scale. If the use of single-use technology was not carefully considered at the start, it can have economical consequences and negatively affect the speed of the development process.
Therefore, you need to determine which single-use technology is most suitable from the very first R&D step. Also discuss this with single-use technology specialists. This is of great importance for the further development of a vaccine. I explain why.
Different vaccines, different production demands
There are about four different types of vaccines:
- Live-attenuated vaccines
- Inactivated vaccines
- Parts of viruses (subunits, polysaccharide, conjugate, recombinant)
- Toxoid vaccines against substances from bacteria
In the (near) future, platform-based viral vectors-vaccines and DNA-vaccines will also be added to this list.
Every vaccine has its own production demands and methods (egg-based, cell-culture, recombinant DNA), so the specifications for the single-use process systems and parts also differ.
Advice is precise work
To say something meaningful about which single-use technology should be used for which type of vaccine, I would have to look at individual production processes. Advice is always based on a case-by-case scenario.
Let me tell you more about the benefits the biopharmaceutical industry is experiencing by using single-use process parts- and systems. It offers greater flexibility, allowing them to switch and scale up quickly. They can prepare production lines to produce a COVID-vaccine easier while meeting the corresponding demands. You also decrease the chance of contamination and influence of the medium by contamination. Single-use systems are replaced after every batch and are not re-used. Extensive and expensive decontamination procedures are not needed. That also saves time. It has helped attribute to the fact that there are already more than 100 different vaccines against COVID-19 in development. Most companies are currently still in the clinical research phase (testing on humans).
Upscale without any problems
To ensure that all steps run smoothly from the research phase on a laboratory scale to scaling up production and to prevent delays, it is therefore important that you think carefully about the single-use products that you will be using from the beginning. After all, the upscale steps must go seamlessly. Imagine that during the upscaling it turns out that the materials that you have used in the lab are not available for large capacities! If you must switch to different single-use materials at that phase, you will have to revalidate and that costs a lot of time. In the worst-case-scenario you must look for a different supplier and audits will have to take place again. Do co-workers from the biopharmaceutical R&D know this and do they keep this in mind? It is worth it to discuss this internally.
Going through the steps
If you contact a single-use specialist at the start of vaccine development, you can discuss all possible steps. This way you will consider all the steps and demands later on in the process. A good example of a single-use product that can be used in different process phases is the AseptiQuik® genderless sterile connector. This connector offers a fast and sterile connection through an easy to use three step design and is available with a wide scale of options in sizes from 1/8 to 1 inch.
So whatever method your company decides to use to produce a vaccine, single-use technology makes the design process more flexible and safer and, in the end, you can set up a single-use production facility faster. Only if you make sure that all phases can seamlessly transition into the next one by keeping this in mind at the start of process. I will gladly help with this